2 min read
Integrated Flow Assurance in Mozambique: A Multi-Software Approach
Jee Ltd
May 16, 2025 2:58:13 PM
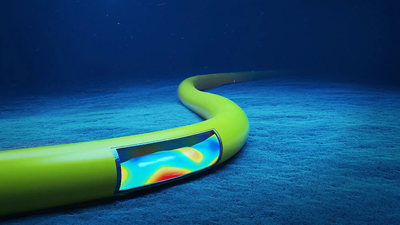
In complex oil and gas developments, flow assurance plays a critical role in ensuring the integrity and efficiency of hydrocarbon transport systems. In one such project in Mozambique, Jee’s Flow Assurance engineers undertook a comprehensive onshore flow assurance study. The project spanned multiple phases of simulation and modelling, requiring the integration of several industry-leading software tools. This case study outlines how the team approached the project using a multi-software methodology, from steady-state analysis to dynamic transient simulations, ensuring robust system design and operability.
The team conducted a FEED project that involved assessing an existing PIPESIM model which was to be used as a base on which to build. The model was used to assess the system at steady state to check if the flowrates and pressures seen would fall within the required operating conditions. The results from these simulations helped to determine the line size for the system.
Following the steady state assessment, the PIPESIM model was benchmarked against and OLGA model so that transient operations could be assessed. Fluid tunning was conducted in Multiflash to help adjust OLGA results to the PIPESIM results.
Once the benchmarking was completed, various transient operations were assessed, including:
- Initial Start-up: Simulations evaluated the system behavior when initiating flow from a non-operational state. This includes tracking pressure buildup, temperature stabilisation, and the risk of hydrate or wax formation due to cold fluids entering the system.
- Turndown: This mode examined system behavior under reduced flowrate conditions. Operating at low throughput can lead to issues such as liquid accumulation, slugging, or unstable flow regimes that may affect system reliability and separator performance.
- Shutdown: Simulations analysed how the system behaves during a planned or emergency shutdown. This includes depressurisation rates, fluid settling, and cooling profiles – all of which impact restart strategies and increase the risk of line blockages.
- Ramp-up: Gradual increases in flowrate were assessed to ensure smooth transitions from lower to higher production levels. This helps verify that equipment can handle dynamic changes without exceeding pressure or temperature design limits.
- Restart (Cold and Warm): After shutdowns, systems may be restarted under different thermal conditions. A cold restart occurs when the system has reached ambient conditions, raising hydrate risks and requiring preheating or inhibition strategies. A warm restart involves less thermal degradation, but still necessitates careful pressure and flow management.
- Pigging: This operation involves running pipeline inspection gauges (pigs) to clean or inspect the line. Transient simulations help determine pressure drops, slug volumes, and fluid dynamics during pig travel to ensure the process doesn’t compromise system integrity or separator efficiency.
This Mozambique project demonstrates the value of a multi-software approach in flow assurance, where steady-state and transient models were integrated to ensure comprehensive system understanding. By leveraging PIPESIM, OLGA, and Multiflash, the engineering team could confidently assess system performance under both normal and transient conditions. These transient simulations allowed visibility of potential flow regimes present at different modes of operation as well as if the current separator design will be sufficient for the system. This also included determining solutions to any separator problems by mechanical or operational solutions.
The result was a well-informed design phase with reduced operational risk and improved system reliability.
For more information, visit www.jee.co.uk/flow-assurance, or call +44 (0)1732 371 371.